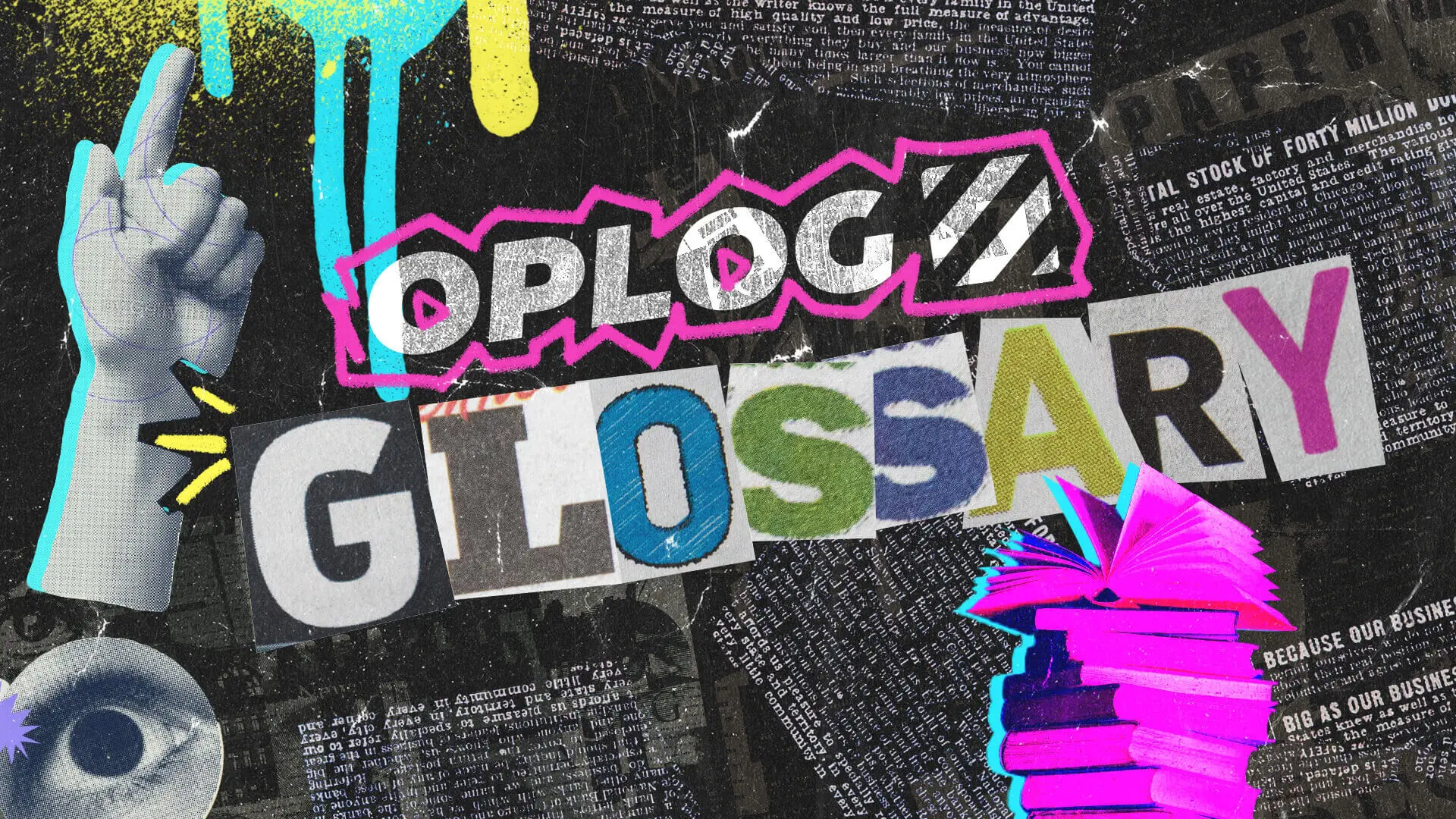
ABC Classification
ABC classification is used in inventory management to categorize items into three categories based on their value and importance.
What is the ABC classification?
ABC classification in warehouses is a technique used to categorize inventory based on its importance or value to the business. This technique helps warehouse managers prioritize their efforts and allocate resources effectively based on the value of the stored items.
The items are classified into three categories:
A-items: These high-value items represent a small percentage of the total inventory but account for a significant portion of the revenue. They are typically high-priced and have a high demand. These items should be closely monitored, and their inventory levels should be kept at a minimum to reduce the risk of overstocking.
B-items: These are medium-value items that represent a moderate percentage of the total inventory and account for a reasonable portion of the revenue. They are moderately priced and have moderate demand. These items should be monitored closely, but inventory levels can be kept slightly higher than A-items.
C-items: These low-value items represent most of the total inventory but account for a small portion of the revenue. They are low-priced and have low demand. These items should be monitored loosely, and inventory levels can be kept higher than A and B items.
Benefits of ABC classification
ABC classification in warehouses offers several benefits to businesses.
Firstly, it helps businesses to better understand and manage their inventory by categorizing items based on their value and importance. This enables businesses to allocate resources, such as storage space, manpower, and equipment, more effectively and prioritize their efforts accordingly.
Secondly, the classification system helps businesses reduce the risk of stockouts and overstocking, leading to lost sales or increased carrying costs.
By identifying high-value items that account for a significant portion of the revenue, businesses can closely monitor and manage their inventory levels to avoid stockouts. At the same time, they can keep inventory levels of low-value items at a higher level to reduce the risk of overstocking.
Thirdly, ABC classification can help businesses to optimize their inventory management processes. For instance, businesses can use classification to determine the most suitable inventory replenishment strategies, such as just-in-time (JIT) or safety stock levels. They can also use it to identify slow-moving or obsolete inventory that needs to be liquidated or disposed of.
Overall, ABC classification in warehouses can help businesses to improve their inventory management processes, reduce carrying costs, and increase profitability. By better understanding inventory, businesses can make informed decisions that lead to more efficient operations and increased customer satisfaction.
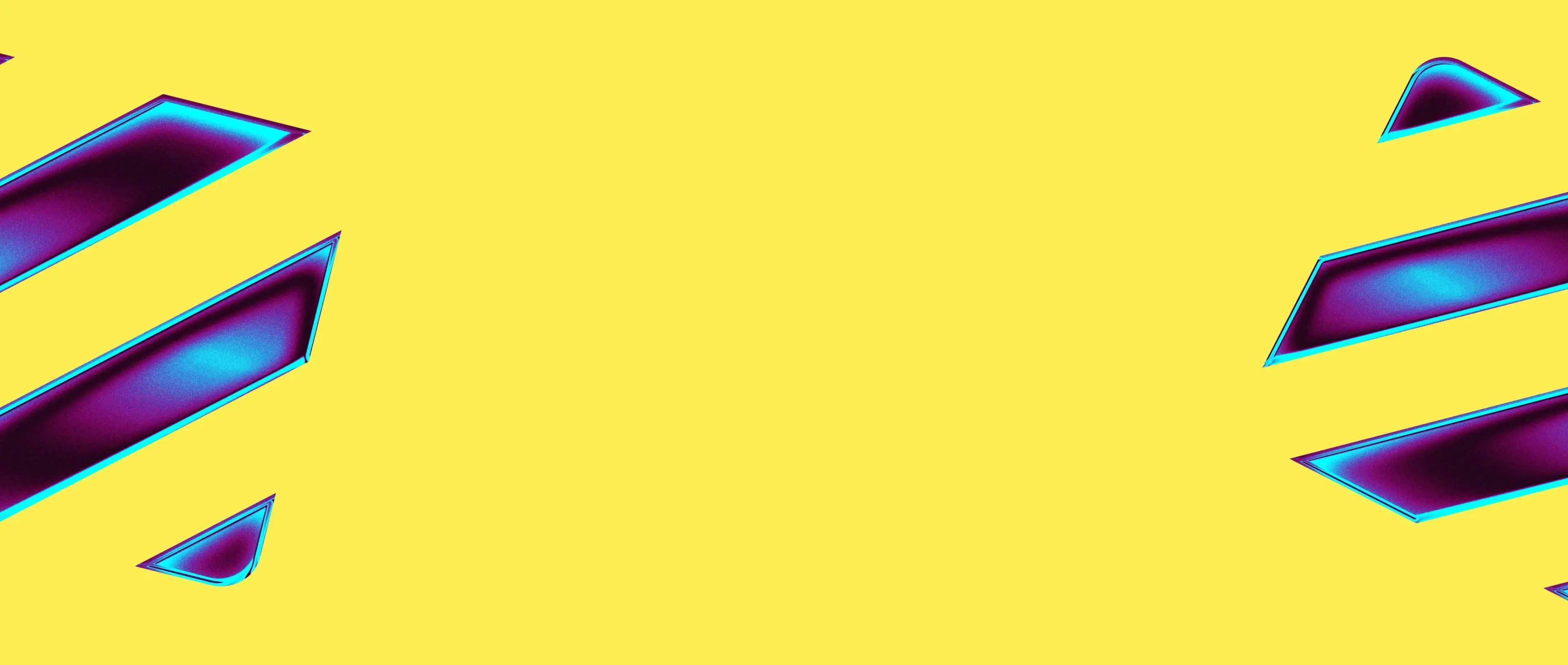