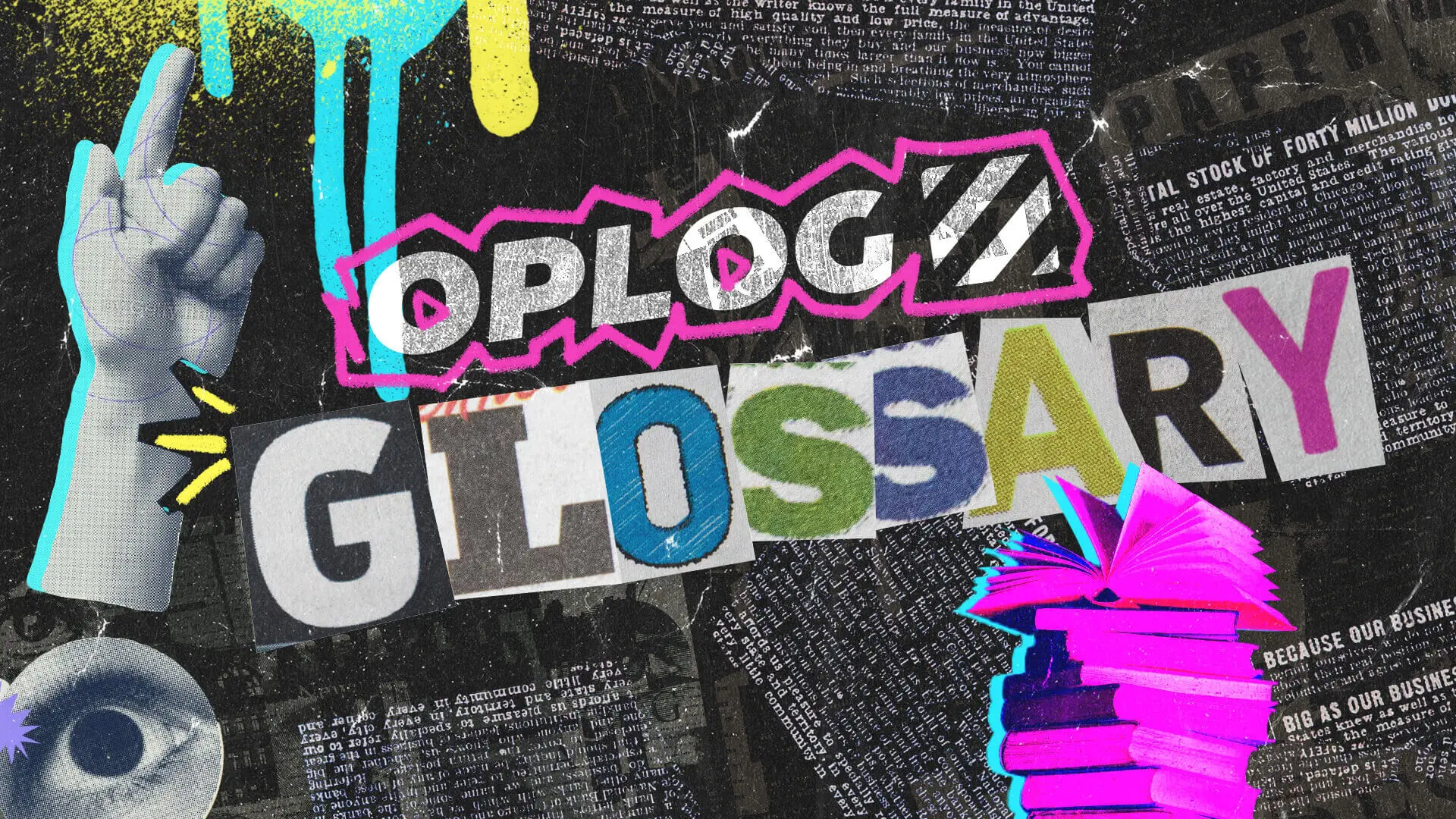
Mispick
A mispick is an error in the order fulfillment process when an incorrect item is picked or pulled from inventory for a customer's order.
What is a Mispick?
Mispick, also known as a picking error or picking mistake, refers to a situation in the order fulfillment process where the wrong item or quantity is picked or selected for a customer's order. It occurs when an incorrect product is chosen from the inventory during the picking or packing process.
Why Mispicks occur?
Mispicks can happen for various reasons, including human error, incorrect labeling or identification of products, inadequate training of warehouse personnel, or problems with inventory management systems. Mispicks can occur in distribution centers, warehouses, retail stores, or any other fulfillment operations where picking is involved.
Negative consequences of Mispick
Customer Dissatisfaction: When customers receive incorrect items, it can lead to frustration, inconvenience, and dissatisfaction. It may result in returns, exchanges, or the need for additional customer service to resolve the issue.
Financial Losses: Mispicks can be financially damaging for businesses. If the wrong items are shipped, the expenses associated with replacing and reshipping the correct ones can pile up. Moreover, if customers opt to return the products due to errors in shipment, additional costs are incurred in the process of restocking or refurbishing.
Operational Inefficiencies: Mispicks disrupt the order fulfillment process and can cause delays in shipping orders. It requires additional time and resources to rectify the mistake, potentially affecting the overall efficiency of the warehouse or fulfillment center.
How to minimize mispicks?
Training and education: Providing comprehensive training to warehouse personnel on proper picking procedures, product identification, and accuracy in order fulfillment.
Quality control checks: Implementing quality control measures, such as double-checking picked items against the order details, using barcode scanning technology, or implementing automated systems that verify item accuracy.
Clear product labeling: Ensuring clear and accurate product labeling, including barcodes, SKUs, or other identifiers that help reduce confusion and mistakes during picking.
Clear product labeling: Ensuring clear and accurate product labeling, including barcodes, SKUs, or other identifiers that help reduce confusion and mistakes during picking.
Order verification processes: Implement order verification processes, such as random or systematic checks by supervisors, to catch mispicks before items are packed and shipped.
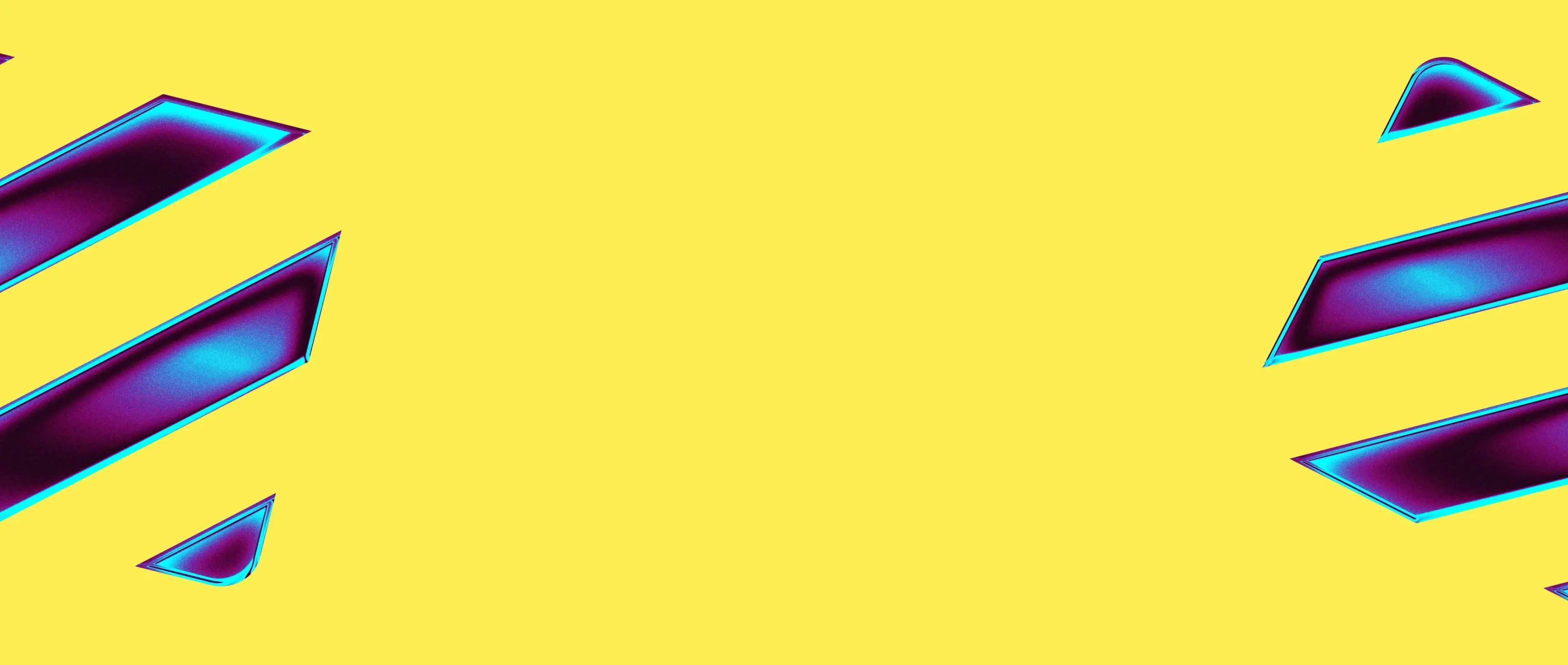