Decoding Warehouse Robotics: Picking, Sorting, and Moving Robots Explained
In today's fast-paced e-commerce landscape, warehouse robots have become essential tools for businesses striving to meet ever-increasing customer expectations. With the global warehouse robotics market valued at $4.31 billion in 2022 and projected to reach $17.29 billion by 2030, according to Grand View Research, these technological marvels are transforming how products move from inventory to doorstep. The days of purely manual warehouse operations are rapidly giving way to sophisticated robotic systems designed to enhance speed, accuracy, and efficiency throughout the fulfillment process.
This transformation isn't just about replacing human effort—it's about reimagining what's possible in logistics operations. Modern warehouse robots fall into three essential categories: picking robots that select items from inventory, sorting robots that organize products for shipment, and moving robots that transport goods throughout facilities. Understanding these distinctions is crucial for businesses looking to develop truly robot-native logistics operations that maximize the potential of automation.
The Evolution of Warehouse Robotics
Warehouse automation has come a long way from the basic conveyor systems of the past. Early automation focused primarily on moving products along fixed paths, offering limited flexibility and requiring significant human intervention. Today's warehouse robots, however, represent a quantum leap forward, featuring artificial intelligence, advanced sensors, and remarkable adaptability.
The explosive growth of e-commerce has been a primary driver of this evolution. As online shopping volumes surged—particularly during and after the global pandemic—fulfillment operations faced unprecedented pressure to process higher volumes of individual orders with greater speed. Traditional manual methods simply couldn't keep pace with these demands, creating the perfect conditions for robotic innovation.
This brings us to the concept of "robot-native" logistics—a philosophy that designs fulfillment operations from the ground up with robotics in mind, rather than retrofitting robots into existing workflows. Robot-native facilities optimize layouts, systems, and processes specifically for robotic efficiency, creating seamless human-machine collaboration rather than forcing robots to adapt to human-centric environments.
Picking Robots: The Precision Specialists
Picking robots represent one of the most transformative technologies in modern warehousing. These specialized machines handle the crucial task of selecting individual items from inventory—traditionally one of the most labor-intensive and error-prone warehouse processes.
The impact of these technologies can be dramatic. Operations that have adopted robotic picking solutions report substantial gains in efficiency, in some cases doubling throughput. Additionally, automation significantly reduces human error, improving order accuracy and consistency. By minimizing mistakes in the picking and packing stages, businesses can better control costs, reduce returns, and enhance overall customer satisfaction—key advantages in a highly competitive fulfillment environment.
Sorting Robots: The Organization Experts
Once items are picked, they need to be organized for shipment—a process that can create significant bottlenecks in high-volume operations. Sorting robots automate this critical function, ensuring that products reach the right packaging station and ultimately the correct customer.
AI-powered sorting systems can adapt to different product types and packaging requirements in real-time, making decisions based on dimensions, fragility, destination, and other factors. This intelligence enables warehouses to handle diverse inventory with a single sorting system, reducing the need for specialized equipment or processes.
The benefits of automated sorting extend beyond speed. By ensuring that the right products reach the right packaging stations, these systems significantly reduce errors that can lead to customer dissatisfaction and costly returns—which typically cost businesses approximately 66% of the original item's price to process.
Moving Robots: The Warehouse Transporters
The third pillar of warehouse robotics focuses on automating the movement of goods throughout the facility. These robots eliminate countless hours of human travel time, allowing employees to focus on value-added tasks rather than simply transporting items from one location to another.
Key Categories of Moving Robots
Two primary types dominate this category:
- Automated Guided Vehicles (AGVs): These robots follow predetermined paths marked by magnetic strips, QR codes, or other guidance systems. While less flexible than their autonomous counterparts, AGVs offer reliability and predictability for standard transport routes.
- Autonomous Mobile Robots (AMRs): Using advanced navigation technologies like SLAM (Simultaneous Localization and Mapping), these robots create their own maps of the warehouse environment and can dynamically plan optimal routes. This adaptability makes AMRs ideal for complex, changing environments.
Both types significantly enhance operational efficiency by reducing manual transportation tasks, leading to improved productivity, reduced worker fatigue, and faster order processing. According to the Deloitte "Warehouse Automation" report, automation in warehousing not only addresses labor shortages but also increases accuracy and reduces cycle times, contributing to overall operational improvements.
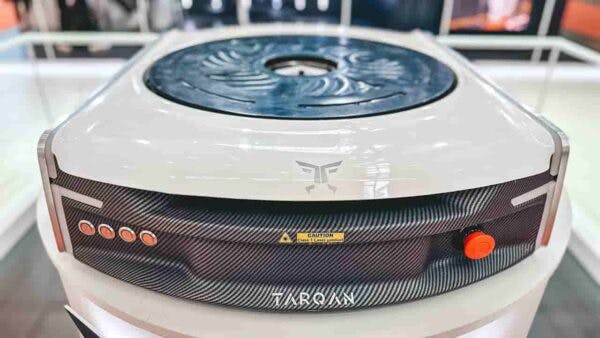
The TARQAN Advantage
In the world of warehouse robotics, most technologies are built to be adapted. TARQAN, on the other hand, was built to lead. Rather than being a plug-and-play solution retrofitted into existing systems, TARQAN was engineered from the ground up with one goal in mind: to power the next generation of robot-native fulfillment. This purpose-built approach gives TARQAN a unique edge—it’s not just a tool within the warehouse; it helps define the warehouse itself. TARQAN is the robotic brainchild of OPLOG, a logistics and technology company that designs and manufactures its own hardware and software to deliver integrated fulfillment solutions. As part of its broader vision to make logistics faster, smarter, and more autonomous, OPLOG developed TARQAN to automate the most repetitive and labor-intensive warehouse tasks, without sacrificing adaptability or system intelligence. What sets TARQAN apart is its native compatibility with warehouse operations that prioritize flexibility and performance. From depalletizing to high-speed sorting and inducting items into sortable systems, TARQAN excels in scenarios where real-time responsiveness and accuracy are critical. With its in-house design, it integrates seamlessly into fulfillment workflows and adapts dynamically to changing inventory and order demands. Field deployments of TARQAN have demonstrated remarkable outcomes: -Up to 300% improvement in operational throughput -Labor efficiency gains exceeding 70% -Order accuracy rates above 99.9% -Substantial reductions in lead times from order to shipment Unlike generalized automation solutions, TARQAN embodies the philosophy of robot-native infrastructure—where robotics aren't an add-on, but a foundation. As e-commerce logistics continues to accelerate and complexity rises, TARQAN represents a clear advantage: custom-built performance at global scale, driven by a company that understands fulfillment from both the physical and digital lens.
Future of Warehouse Robotics
The evolution of warehouse robotics shows no signs of slowing. Several emerging trends will likely define the next generation of these technologies:
Advanced AI and Machine Learning
Future robots will demonstrate increasingly sophisticated decision-making capabilities, moving beyond programmed responses to true adaptability. These systems will predict and prevent potential issues before they affect operations.
Enhanced Computer Vision
Improvements in visual processing will enable robots to identify and handle an even wider range of products with minimal pre-programming, adapting to new inventory without extensive setup.
Greater Human-Robot Collaboration
Rather than replacing human workers entirely, next-generation robots will focus on augmenting human capabilities, handling repetitive or physically demanding tasks while people focus on complex problem-solving and customer service.
Sustainability Improvements
Optimized robotic systems will contribute to greener warehousing by reducing energy consumption, minimizing waste through greater accuracy, and enabling more efficient use of space and resources.
By 2029, same-day and next-day delivery will likely become the standard expectation rather than a premium option. Meeting these expectations will be virtually impossible without sophisticated robotic systems managing the fulfillment process.
Key Takeaways
- Warehouse robots fall into three main categories: picking robots that select items, sorting robots that organize products, and moving robots that transport goods throughout facilities.
- Robot-native logistics operations design processes from the ground up to maximize the efficiency of human-robot collaboration.
- Significant ROI comes from multiple sources: reduced labor costs, improved accuracy, increased throughput, and enhanced scalability.
- The future belongs to integrated systems that combine multiple robotic functions within unified platforms like TARQAN.
- Implementation should be strategic, considering integration requirements, scalability needs, and staff training.
Conclusion
The warehouse robotics revolution isn't just changing how products move through fulfillment centers—it's fundamentally transforming what's possible in e-commerce logistics. By automating picking, sorting, and moving functions, these technologies enable levels of speed, accuracy, and efficiency that would be unattainable through manual processes alone.
For businesses looking to remain competitive in an increasingly demanding market, understanding and implementing the right mix of robotic technologies isn't just advantageous—it's becoming essential. As customer expectations for rapid, accurate delivery continue to escalate, the question isn't whether to adopt warehouse robotics, but which solutions will best support your specific business needs.
The most successful operations will be those that embrace a robot-native approach, designing their fulfillment processes to maximize the unique capabilities of these technologies while maintaining the human expertise and oversight that remain invaluable. In this harmonious collaboration between human and machine, we find the future of logistics excellence.